The Elegant Journey of Satin Ribbon: From History to Modern Uses
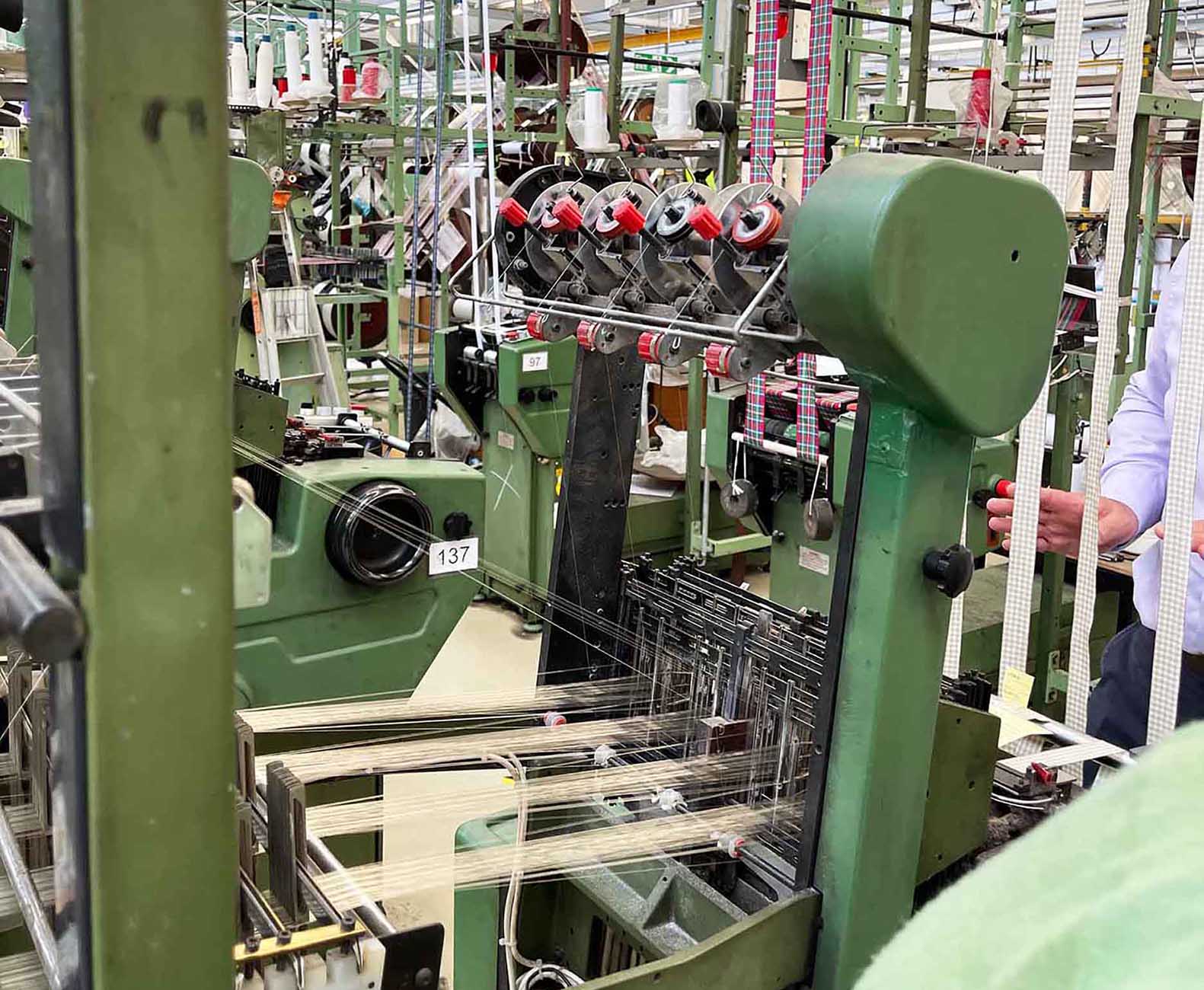
Satin ribbon, with its luxurious sheen and smooth texture, has long been a favorite in the world of crafting, fashion, and decor. Its elegance and versatility make it a staple in everything from gift wrapping to haute couture. In this article, we’ll explore the rich history of satin ribbon, its intricate manufacturing process, and the differences between single satin and double satin. We’ll also delve into the unique world of wired satin ribbon and its myriad uses.
A Brief History of Satin Ribbon
The origins of satin can be traced back to the Middle Ages, specifically to the city of Quanzhou in China. The fabric was originally made from silk and was known for its glossy surface and dull back. The word "satin" itself derives from the Arabic word "zaytuni," which refers to the Chinese port city of Quanzhou. Satin made its way to Europe through the Silk Road and quickly became a symbol of luxury and sophistication.
During the Renaissance, satin was highly sought after by the European elite, often used in the creation of opulent garments and accessories. As time progressed, the use of satin expanded beyond clothing, finding its place in home decor and, eventually, in the form of ribbons.
The Intricate Manufacturing Process of Satin Ribbon
Creating satin ribbon is a meticulous process that begins with the careful selection and preparation of threads. Here's a closer look at how these elegant ribbons are made:
1. Thread Preparation: Threads are wound onto large spools which are placed on frames known as creels. This preparation is crucial as it ensures that the threads are properly aligned and tensioned for the weaving process. The threads must be uniform in thickness and strength to produce a consistent and high-quality ribbon. There can be up to 600 spindles on each creel depending the width of ribbon that they are looking to weave.
(Above: Taking the threads from spools through the creel & on to a warpping beam)
2. Warping: Once the threads are wound on the creels, they are then warped onto a beam. Warping is a process where threads are arranged parallel to each other, forming the warp that will be woven into ribbon. This stage requires precision to ensure that the threads do not tangle or break. Every thread has to be individually pulled through from there spool along the creel frame to the warping beam. This can be a lengthy process to set up.
3. Weaving: The weaving process involves interlacing the warp threads with weft threads on a loom. The satin weave technique, characterized by floating warp threads over weft threads, creates the signature glossy surface of satin ribbon. This weaving method gives satin its smooth texture and elegant appearance.
Satin Ribbon Being Woven On A moden Loom
4. Dyeing: Most satin ribbons are initially woven using plain white or neutral threads. These ribbons undergo a bulk dyeing process, where they are immersed in large dye baths to achieve the desired colour. This method ensures even colour distribution and allows for vibrant, long-lasting hue.
Dyed Ribbon Being Washed & Dryed
5. Finishing: After dyeing, the ribbons undergo a finishing process that enhances their sheen and texture. This involves treating the ribbons with special finishes that add luster and softness, making them ready for various applications.
Embracing Sustainability: Recycled Polyester in Satin Ribbons
In recent years, there has been a significant shift towards sustainability in the textile industry. Satin ribbons are no exception, with many manufacturers now using recycled polyester threads. These threads are made from recycled plastic drink bottles, offering an eco-friendly alternative to traditional materials.
The process of creating recycled polyester involves collecting and cleaning plastic bottles, which are then shredded into small flakes. These flakes are melted and extruded in to fine thin threads which in turn are spun into yarn, which is then used to weave satin ribbons. This innovative approach not only reduces waste but also conserves resources, making satin ribbons more environmentally friendly.
Single Satin vs. Double Satin: What’s the Difference?
One of the most common questions about satin ribbon is the difference between single satin and double satin. The distinction lies in the weaving process and the resulting texture and appearance.
Single Satin Ribbon: This type of satin ribbon features a glossy finish on one side and a matte finish on the other. It is often used for applications where only one side of the ribbon will be visible, such as wrapping gifts or tying bows. Single satin is typically more cost-effective than double satin, making it a popular choice for everyday use. It’s popular for packaging as it ties well as the slight texture to the reverse of the ribbon means that bows and knots hold well and stay in place.
Double Satin Ribbon: As the name suggests, double satin ribbon boasts a glossy finish on both sides. This is achieved by weaving the ribbon in such a way that both sides exhibit the same luxurious sheen. Double satin ribbons are ideal for projects where both sides of the ribbon will be visible, such as in fashion design or intricate crafts. They are often considered more luxurious and are priced accordingly. However in recent years the demand for Double Satin finishes has increased dramatically, as a result the cost of making and supplying this ribbon finish compared with the single satin has reduced and now the too can be purchased at similar price points.
Wired Satin Ribbon: Adding Structure to Elegance
Wired satin ribbon is a versatile variant that incorporates thin, flexible wires along the edges of the ribbon. This addition allows the ribbon to hold its shape, making it perfect for creating structured bows and elaborate decorations. The wire is discreetly integrated into the ribbon, maintaining its elegant appearance while enhancing its functionality.
Whilst wire is used in the manufacture of most of these ribbons, there are some variants available where the wire has been substituted for a plastic filament. This has similar benefits to the wire, and one main overarching benefit, this being it will not rust if it gets wet making it very attractive for certain applications.
Uses of Wired Satin Ribbon:
- Gift Wrapping: Wired satin ribbons are ideal for creating elaborate bows that retain their shape, adding a touch of elegance to any gift. As the wire helps the ribbon hold the shape that it has been tied in to.
- Floral Arrangements: The ability to shape and mould wired satin ribbon makes it a favourite among florists for adding decorative touches to bouquets and arrangements. This style of ribbon also tends to come in wider widths which helps the florist make statement pieces more easily.
- Home Decor: From wreaths to table settings, wired satin ribbon can be used to create stunning decorative elements that maintain their form.
- Event Decor: Wired satin ribbons are often used in weddings and other events to create beautiful, structured decorations that enhance the overall aesthetic. Again the wired edges mean that wider ribbons can be used as the wire supports the added weight of the extra fabric and stops it flopping, helping to create great decorative features.
Leading Manufacturers: A Nod to Tradition and Innovation
While there are many large manufacturers of satin ribbon worldwide, the UK boasts one of the oldest and most renowned—Berisfords. Known for their quality and craftsmanship, Berisfords has been producing ribbons for over a century, blending traditional techniques with modern innovations to meet the evolving demands of the market. They offer an extensive range of satin ribbons in over eight shades and eight different ribbon widths. Recently they have been one of the European manufacturers to make the transition from virgin polyester yarns to fully recycled polyester thread instead. As a result this is our main satin ribbon range of choice and one that we try and hold in stock.
When Does A Ribbon Become A Fabric
Satin ribbons come in a wide range of widths from the very narrow 2mm width sometimes known as rats tail through to the wide 70mm ribbons.
We are often asked what is the widest satin ribbon that we stock, the answer to this is the 100mm (10cm wide) single satin ribbon. This is the widest woven edge ribbon that we can get made. There are ribbons that are wider but rather than being true ribbon with woven edges (finished in this way so that the weave does not fray), the wider lengths are really fabric stripes that have been cut in to lengths. These tend to have hot cut slit edges which stop the woven fabric from fraying to a degree. However, these have been woven as a fabric sheet which have then been slit into strips rather than woven as a specific ribbon. The 100mm ribbons are widely used for sashes and banners.
Above: A 100mm wide ribbon which we print for Aldi to use for store launches
Conclusion
Satin ribbon, with its rich history and versatile applications, continues to be a beloved material in various creative fields. Whether you’re choosing single satin for a simple project or double satin for a more luxurious touch, understanding the differences and uses of each type can enhance your crafting experience. Wired satin ribbon, with its added structure, opens up even more possibilities for creativity.
Embrace the elegance of satin ribbon in your next project and enjoy the timeless beauty it brings. Whether it’s for a special occasion or everyday use, satin ribbon adds a touch of sophistication and charm that never goes out of style.